Speaking of decisions - I am building a base for a dining room table, and although my clients give me a rough idea of they want, there are still a multitude of design decisions to make.
Here's a rough full-sized sketch on a piece of cardboard of what I am building.
I prepped the African mahogany to size, planing it and cutting it to length and width. Then I cut the tenons on the top and bottom.
But before I can go much further, I need to make a plywood template of the curve that will be cut in each piece. That's where a beam compass like this comes in really handy.
I know that the diameter is roughly 18", so I set the beam compass to half that, or about 9".
The plywood is cut to the exact size of my mahogany panels.
Here, the semi circle is drawn on the plywood.
I have a spare router base with a piece of plywood attached to it. This allows me to use the router as a giant compass. The curves you cut by hand, with a jig saw or a bandsaw, will never achieve the perfection of one cut with a router and compass. Trust me, I've tried it many times.
Here is a quick video on using this compass set-up, to cut a pattern. Then, I'll use the pattern to rout all the parts. Sound complicated? Just watch the video - it's easy!
Here is the pattern, trimmed up a little bit, so that it mimics the shape I want to wood to be cut into.
Use a straight bit in your router, with a template guide bushing.
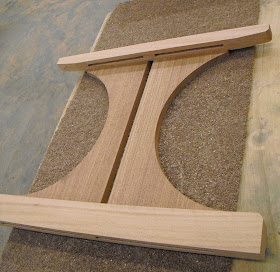
This bottom transition area really bothers me - it looks clunky and doesn't fit in with the rest of the piece.
Thinking on the fly is a must when you get to this stage of the game. I made a few sketches, and came up with a curve that I think works better. Making a pattern of it was easy - I just cut up a piece of that larger template, and made a small pattern to use. Here is it, clamped to the leg base.
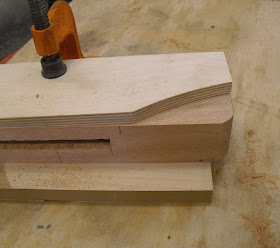
Since the wood is nearly 2" thick, it had to be routed in several passes.
And I needed to pull out the big gun - a 3" straight bit for my router. Actually, it was easier to use two routers - one with a short bit, and one with a long one.
This bottom transition area really bothers me - it looks clunky and doesn't fit in with the rest of the piece.
Thinking on the fly is a must when you get to this stage of the game. I made a few sketches, and came up with a curve that I think works better. Making a pattern of it was easy - I just cut up a piece of that larger template, and made a small pattern to use. Here is it, clamped to the leg base.
Since the wood is nearly 2" thick, it had to be routed in several passes.
And I needed to pull out the big gun - a 3" straight bit for my router. Actually, it was easier to use two routers - one with a short bit, and one with a long one.
Routing makes a ton of dust, make sure you wear a mask and sweep up the floor afterwards, or you'll just keep kicking those particles into the air.
And finally, the finished shape. One I can live with. I'm still going to tweak that area right above where the curve starts, rounding it over to eliminate that sharp corner.
Here is one of the ends; it just needs a little sanding and it will be ready to assemble. Later, I'll connect both ends with two stretchers. Hopefully, my clients will be sitting at their table in time for Thanksgiving!
I hope this post illustrates the fact that designing on the fly is a necessary part of the craft. You can come up with all the plans you want on paper, but until you see them machined on the wood, it's hard to know if they work or not. Each step of the process allows you to see more, and if you spot something that looks wrong, you can correct it.
That's what I love about wood - the forgiving nature of it.
Awesome technique, and gorgeous results. Thank you for posting this Jamie!
ReplyDelete